In order to effectively showcase the individual components that would eventually comprise the final instrument, I took the initiative to create a rudimentary version resembling a Hackbrett, utilizing a wooden board and a Floyd Rose tremolo system. This makeshift instrument boasted the inclusion of two strings and a mobile bridge, enabling the manipulation of string pitch without the need for mechanical screws.
To emulate the motion of drumsticks required to play the instrument, I employed two piano hammers (Fig. 2) upon which I strategically positioned the two solenoids. These solenoids were connected to the structure through the help of a wooden stick, which also served as a housing for all the necessary electronic components (Fig. 1), ensuring a compact and conveniently transportable design. The resultant outcome was an instrument that facilitated effortless customization, thanks of its adaptable elements capable of being repositioned in space, thereby opening up a realm of diverse tonal possibilities to be explored.
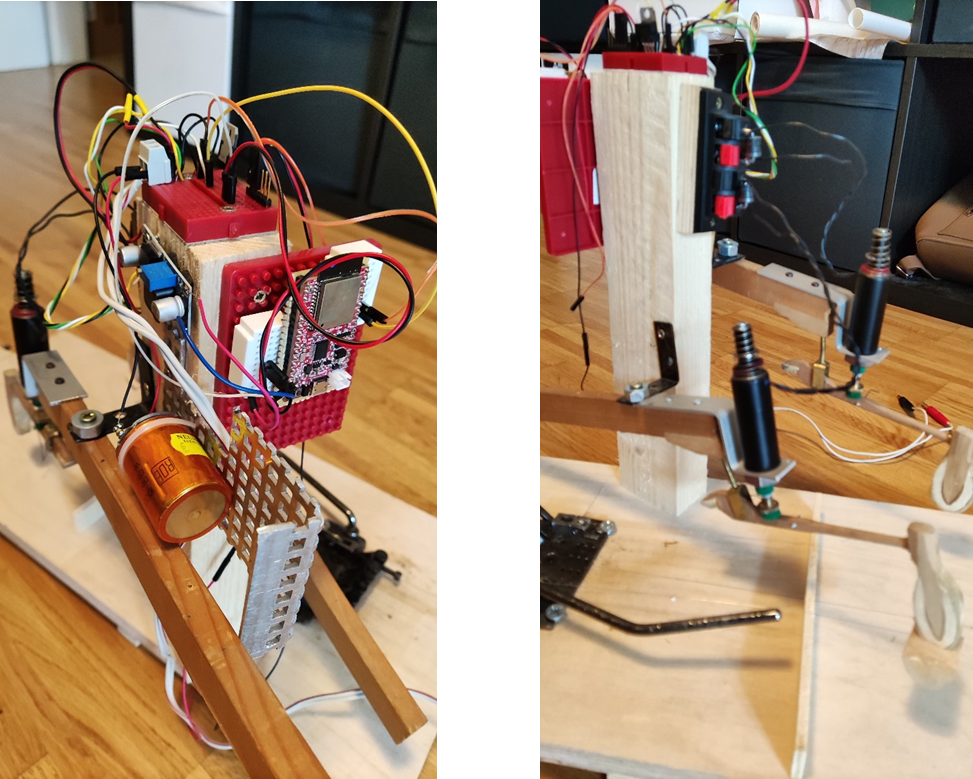
The decision to use wood as the primary material for the instrument was driven by its acoustic characteristics. Even without the presence of a resonance chamber, wooden material offered a sound quality that closely resembled the desired outcome of the final product.
To capture the sound produced by the strings, I opted for an electric piezo system. This allowed for the isolation of the direct string sound from the mechanical sound generated by the solenoids. By employing this setup, I could accurately capture the nuances of the instrument’s natural vibrations while maintaining control over the mechanical elements. To amplify it, I mounted a speaker on a wooden plate that should has work as resonator. The entire amplification id driven by a D-Class amplifier PAM480[1], attached with the speaker directly on the body of the instrument (Fig. 3).
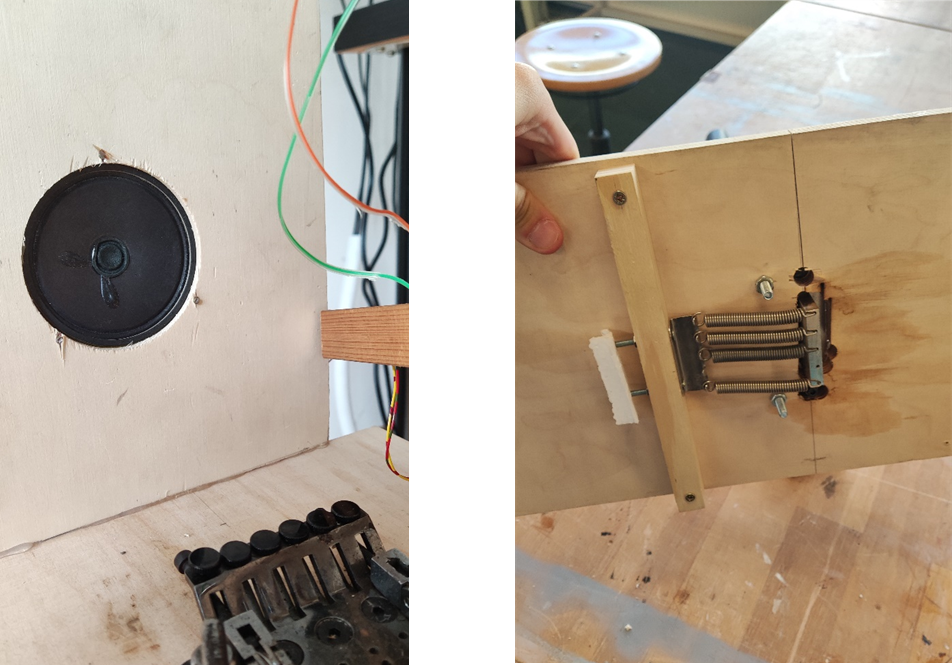
By fixing the Floyd Rose lever (Fig. 4) in conjunction with the stepper motor, I devised a solution using two small wooden pieces that served as a guide for the lever. This setup ensured that the lever remained stable and fixed during the tensioning process. Strategically positioning the stepper motor directly at the tip of the lever was a deliberate choice aimed at maximizing the advantage of leverage. By identifying the optimal leverage point, I could effectively exert tension on the strings with minimal effort from the stepper motor.
Regarding the use of the Servo motor, the idea is to simulate a feature of the final instrument that will be applied during the next semester, i.e. a mute that can attenuate the strings. As can be seen in Fig. 5, the pedals are connected by a string to a wooden rod and felt, which acts as a mute if necessary.
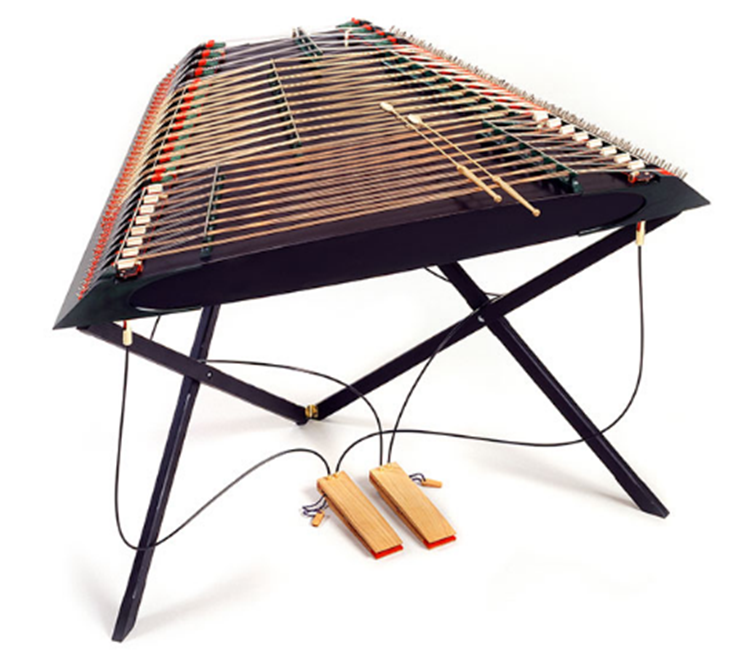
[1] GmbH, B. 73 A. (no date) Startseite, Startseite • FUNKAMATEUR OnlineShop. Available at: https://www.box73.de/product_info.php?products_id=4391 (Accessed: 15 June 2023).